Closed Loop Partners Releases First-of-its-Kind Report Evaluating the Role of Molecular Recycling Technologies in Addressing Plastic Waste
November 17, 2021
New report examines economic, environmental and human health impacts of diverse recycling technologies, assessing where they fit in a circular plastics economy
November 17, New York – Today, Closed Loop Partners’ Center for the Circular Economy released its latest report, Transitioning to a Circular System for Plastics: Assessing Molecular Recycling Technologies in the United States and Canada. This research fits into the firm’s broader Advancing Circular Systems for Plastics & Packaging Initiative, which tackles plastic waste through innovation and investment; prioritizing design innovation and reuse models to reduce the overall volume of plastics produced, while also strengthening recycling infrastructure to recover existing plastics after use. This new report focuses specifically on one part of the recycling system: “molecular” or “advanced” recycling technologies. It examines their potential role in a circular and safe future for plastics, and the policy, market, and environmental and human health impact conditions needed to achieve this optimal future state.
The sheer diversity and volume of plastics in our system today, from textiles to packaging to electronics, means that no single sector, technology or approach can solve the plastics waste challenge entirely or quickly enough. Plastics production is set to triple by 2050; to move the needle on the 9% of plastics currently recycled globally, a suite of solutions must be deployed, first emphasizing reduction and reuse, and also acknowledging the role of recycling in keeping valuable plastics in play for longer and reducing the need for fossil fuel extraction.
Molecular recycling, also commonly referred to as advanced recycling or chemical recycling, refers to a diverse sector, which encompasses dozens of technologies that use solvents, heat, enzymes, and even sound waves to purify or transform plastics at the molecular level. While these technologies require more energy than traditional mechanical recycling, they can process a wider range of plastic waste into like-new materials. Their various outputs can be looped back into manufacturing supply chains without compromising quality or being downcycled.
Collectively, molecular recycling technologies have the potential to expand the scope of plastics we can recycle, help preserve the value of resources in our economy, and help meet the demand for high-quality, recycled plastics, even food grade plastic. However, to date, there is a scarcity of comparative analysis among the different technologies and a lack of systems-level analysis of their potential financial, environmental, and human health opportunities and risks.
In Assessing Molecular Recycling Technologies in the United States and Canada, Closed Loop Partners goes deeper into many of the unanswered questions regarding these technologies, committing to support data-backed decision-making in this early-stage sector. Together with its technical partner Anthesis Group, Closed Loop Partners worked with nine companies – APK AG, PureCycle Technologies, Carbios, GreenMantra, JEPLAN, gr3n, Brightmark, Plastic Energy, and Enerkem – across the sector’s three molecular recycling technology categories: purification, depolymerization and conversion. The report shares insights drawn from the evaluation of the nine datasets, with the goal of educating investors, brands, retailers, policymakers and nonprofit organizations that seek actionable information on the sector.
“To close the loop on plastic waste we will need to deploy multiple strategies and harness innovation in reduction and reuse alongside a diversity of recycling technologies. It’s imperative that we recover all kinds of plastic, including and beyond single-use plastic packaging. Two-thirds of plastics used in the U.S. today are for applications like wind turbines, textiles, car parts and healthcare devices––which are viable feedstock for different advanced recycling technologies,” says Kate Daly, Managing Director of the Center for the Circular Economy at Closed Loop Partners. “This report should serve as a guide to investors, policymakers, and anyone who cares about the plastic waste crisis and would like to explore what must be true in order for new and established technologies to play a safe and viable role in a circular system for plastics, without creating unintended consequences.”
The report includes 10 key takeaways and calls to action for stakeholders to advance safe and circular solutions to address the urgent plastic waste crisis. Key insights from the report include:
- Overall, the average carbon emissions from producing plastic through all three molecular recycling technology categories showed an improvement compared to corresponding virgin plastics systems, with environmental impacts varying within and across the technology categories
- A greener grid will play a critical role in decreasing the environmental impact of these technologies and renewable energy inputs should be integral to any commercialization strategy of technologies looking to link to the circular plastics economy
- Molecular recycling technologies can complement existing mechanical recycling infrastructure by processing plastic waste that mechanical recyclers would otherwise have to pay to discard; integrating a mix of all three molecular recycling technologies into the broader recycling system in the United States and Canada could double the amount of plastic packaging recycled, compared to 2019 recycling rates, and generate up to $970 million dollars (USD) annually for the existing recycling system
- Policymakers, investors, and businesses, among other key stakeholders, will determine the degree of environmental, human health, and financial success of this sector; they are responsible for ensuring that the most circular solutions are scaled, incentives are established to support circular outcomes, and policies and regulations maintain and protect human health, worker safety, and climate change mitigation
This report includes over 100 questions to supplement an investor’s due diligence of molecular recycling technologies, as well as links to nine case studies that outline best-practices in the market today. To download Closed Loop Partners’ latest report and sign up for educational webinars on the topic, please visit the Closed Loop Partners website here.
About Closed Loop Partners
Closed Loop Partners is a New York-based investment firm comprised of venture capital, growth equity, private equity and project finance, as well as an innovation center focused on building the circular economy. The firm has built an ecosystem that connects entrepreneurs, industry experts, global consumer goods companies, retailers, financial institutions and municipalities. Investments align capitalism with positive social and environmental impact by reducing waste and greenhouse gas emissions via materials innovation, advanced recycling technologies, supply chain optimization and landfill diversion. Learn more here.
About Advancing Circular Systems for Plastics and Packaging Initiative
At Closed Loop Partners, we envision a waste-free future for plastics. We launched our Advancing Circular System for Plastics and Packaging Initiative understanding that there is no silver bullet solution to solve complex global waste challenges. Ending plastics waste will require a combination of approaches such as design innovation, reuse and molecular recycling to accelerate the transition to a circular economy for plastics. Learn more about our investments, collaboration and research here.
This report, Transitioning to a Circular System for Plastics: Assessing Molecular Recycling Technologies in the United States and Canada, focuses on one part of a circular plastics system: molecular recycling technologies. Our Center for the Circular Economy created this report with the support of nine molecular recycling technology companies, more than 75 peer reviewers and advisors, NGO partners and contributing partners Target Corporation, Bank of America Foundation, Colgate-Palmolive Company, the American Chemistry Council, 3M & Sealed Air Corporation.
Going Beyond Single-Use Packaging to Address All Plastic Waste
November 13, 2020
At Closed Loop Partners, we recognize the need to deploy multiple strategies to build a system that addresses all kinds of plastics. In a world of interdependent, global supply chains, plastic waste is the responsibility of every industry and country around the world. While activism and industry action primarily focuses on single-use plastic packaging, have we been myopic in our framing of the problem?
We are overlooking the equally visible plastics that are just as challenging to recover and reuse: the plastics that make up half the volume of every car; the plastics that make up 20 percent of the 55 million tons of electronic waste sent to landfill annually; the polyester (plastic) that represents 60 percent of all apparel fibers; and 42 percent of all non-fiber plastics which go to packaging. While we’ve developed recovery systems for some plastic packaging, we’ve failed to see the challenge holistically, in ways that address diverse forms of plastics in our system. Meanwhile, they have been steadily mounting in landfills, with limited to no end-of-life solutions.
The reality is that we need to solve for and build systems to prevent, reduce, reuse or recycle all plastic waste, not just packaging. Across industries and sectors, we must deploy all tools available to build a circular system for plastics. These include: harnessing design innovation to eliminate unnecessary plastic and reduce extraction of fossil fuels; scaling reuse systems and rental and resale platforms; investing in mechanical recycling and designing products that align with that system; and investing in advanced recycling technologies that can safely transform hard-to-recycle plastic waste into valuable new products or into building blocks to make new plastic or packaging.
Focusing on a single strategy to the plastic waste challenge compounds risks.
While solutions such as reuse and rental systems are critical to extending the life of a product, they are not necessarily plastic-free systems. Companies such as Rent the Runway allow users to subscribe to a library of clothing, allowing thousands of garments to be shared by 8 million customers. Even so, after dozens or even hundreds of uses, a clothing item likely will need to be retired, but currently no widely available, commercial recycling solutions exist to capture that textile waste. Even the most innovative companies leveraging reuse models for cups, food delivery or personal care packaging include some plastics or other valuable materials in their packaging or services that after many uses will need recycling. These solutions are a small part of supply chains today, but we believe they have a strong opportunity for growth. And as they continue to grow, it is important to think ahead about solutions for the ends-of-life of materials in these systems, to keep them in circulation.
If we consider mechanical recycling, plastics that undergo this process can run through it only about seven times before becoming too degraded, and mechanical technologies cannot process most of the 16.9 million tons of textile waste Americans send to landfill every year.
The current strategies to address plastic waste are complementary, but taken alone they will be ineffective at producing a circular system for plastics. Without a multi-pronged approach, we will continue to see growing stockpiles of plastic waste in all forms, from various industries. We are at a critical moment of consensus. Across industries and sectors, stakeholders agree that we want and need reduction in plastic and better management of the plastics being produced. Enabling these outcomes will require policy shifts, incentives, investment, education and long-term partnerships. And we will need to experiment with and invest in emerging and nascent solutions that can safely solve for difficult material types.
Advanced recycling technologies can contribute one piece to the puzzle, solving for our hardest-to-recycle plastic-based products, such as healthcare-related plastics, multi-layer packaging, apparel and building materials.
Like the plastic waste problem, there is a tendency to oversimplify advanced recycling. It is not a monolith; rather, it is a sector marked by distinct and diverse technology processes that purify or break down plastic to create virgin-quality outputs through a number of biological, thermal and/or catalytic processes including dissolution, glycolysis, pyrolysis and gasification. Closed Loop Partners has categorized these processes into three buckets: purification; decomposition; and conversion. Some technologies, such as pyrolysis, have been around for decades. Others are new and developing; all are improving and not all will be winners. Like anything, it is a growing and competitive landscape and those that are the most cost-effective with the most positive environmental impact likely will advance quickly.
Two very different stories emerged this week around advanced recycling technologies. Purecycle, a purification company, just closed a $250 million bond for its Ohio facility, after successfully proving its technology at scale by processing discarded carpet into clear, high-quality polypropylene. Meanwhile, another advanced recycling technology company, LOOP Industries, was put under the spotlight by a research firm for failing to meet expectations. The stories around Purecycle and LOOP Industries show the importance of deep due diligence and the need for continuous testing and honing of solutions to de-risk them before scaling. We’re continuing to evaluate purification, decomposition and conversion technology processes, their environmental and human health impacts, supply chain economics and policy landscape. The technology processes themselves do not determine whether a company or a process is “circular.” The stakeholders invested in creating circular systems do.
While we’ve developed recovery systems for some plastic packaging, we’ve failed to see the challenge holistically, in ways that address diverse forms of plastics in our system.
Historically, market incentives and policies have not favored circular outcomes from advanced recycling processes. In the United States, manufacturers are not rewarded for using recycled plastic, nor are they penalized for using virgin sources. This has meant that manufacturers have favored the lowest priced commodity on the market, often virgin plastics, and the economics for advanced recycling have bent towards supplying industry with fuel produced from plastics. However, mandates that require recycled content, brand commitments to use post-consumer recycled content for their products and packaging, and landfill bans are becoming more prevalent across diverse markets, increasing the demand for high-quality recycled plastic.
The biggest economic and environmental opportunity in advanced recycling is to build circular supply chains for plastics, meaning plastic-to-plastic loops, which ensure that we keep materials at their highest value within our economy for as long as possible. We can align the advanced recycling market towards circular principles by creating market incentives and supportive policies that recognize these technology processes as recycling when their outputs are directly looped back into plastic supply chains.
Are there unknowns related to these new technologies or processes? Yes. It’s critical that we gain a better collective understanding of the environmental and human health impacts of these recycling processes. We must understand what conditions need to be true to steer the industry towards a circular economy, or risk perpetuating a linear system. Closed Loop Partners is leading a research project with this type of impact assessment as one central objective of our study, alongside an assessment of collections and feedstock processing, and investment guidelines to align this sector to circular principles.
It took the solar industry 40 years to reach 1 million solar systems in the United States, but three years after hitting the 1 million mark in 2016, the U.S. surpassed 2 million systems. In 2010, only 4 percent of new electric capacity was solar, but by 2016, it was 40 percent. Technology development and building an industry around a novel technology takes time, incentives and long-term partnerships to drive investment and scale. Advanced recycling will be no different, and because the sector is newly developing, all stakeholders — brands, retailers, investors, plastic producers and recyclers, NGOs and citizens — have the opportunity and a role to play to ensure a safe and circular system and future.
In 2020, we are continuing our research in the sector to understand the environmental and human health impacts of advanced recycling processes, the policy measures and investable opportunities along the supply chain that can enable a circular future for plastics and a safe and sustainable future. We invite you to learn more about our work on advanced recycling here.
Originally published on GreenBiz.
Balcones Resources Acquires Florida’s First AI-Powered Recycling Company Single-Stream Recyclers to Expand & Modernize Best-in-class Recycling Facilities in the U.S.
August 06, 2020
Closed Loop Partners, Balcones Resources and Single Stream Recyclers Come Together to Advance the Circular Economy Ecosystem in the South
Austin, Texas (August 6)- Balcones Resources, an Austin-based environmental services company, backed by leading circular economy investment firm Closed Loop Partners, announced today the acquisition of Single Stream Recyclers (SSR), Florida’s first artificial intelligence- (AI-) powered recycling facility based in Sarasota, Florida. This represents the growing footprint of best-in-class recycling facilities in the South focused on updating, optimizing and reinvigorating recycling infrastructure in the United States to keep valuable materials – paper, plastics, and metals – in manufacturing supply chains.
“Bringing Single Stream Recyclers into the Balcones orbit moves us several leaps forward in our shared vision to scale modern, innovative recycling infrastructure to build circular supply chains. The energy, integrity, and expertise that SSR’s operators bring to the table will only enhance our playbook and bring our specific level of excellence to more markets,” said Joaquin Mariel, COO of Balcones Resources.
Single Stream Recyclers focuses on processing recyclables from residential and commercial single-stream programs within the Florida market. The company is on the forefront of modernizing recycling by pioneering advanced technologies, including AI, robotics and optical sorters. The facility currently has 14 robots installed, using the AMP Robotics system, to increase the efficiency of sorting and the quality of recycled materials; in turn transforming the economics of the recycling system.
John Hansen and Eric Konik, founders of SSR and industry veterans, have been working together since 2006 to modernize the recycling industry. They have more than 50 years of combined experience in recycling, with a deep expertise in building and operating best in class facilities that create bales of commodities ready to go back into packaging and product supply chains. They are known for their successful hands-on approach to growing recycling facilities, with expertise and insight into how each division of an organization functions together.
“We built SSR as we saw a huge need for improved recycling infrastructure with more efficient processing capabilities. With the growing demand from companies for high quality recycled content, it is time to build the materials recovery facilities of the future that will be the hubs of these supply chains. In partnership with our friends at Balcones and Closed Loop Partners, we can scale the systems needed to realize that circular vision,” said John Hansen, Co-founder of SSR.
Balcones Resources is a best-in-class recycling and resource management company that has been in business for more than 25 years, handling commercial and residential recycling, among other services in Texas and Arkansas. Balcones was looking for a partner that would bring the same level of operational excellence and long-term relationships to help expand into new markets.
“Single Stream Recyclers is a valued community partner and has the kind of experience and operational knowledge that aligns with our organization’s management team. Together we will be able to offer state-of-the-art equipment and innovative technology that will help us continue to revolutionize the recycling industry,” said Kerry Getter, Chairman and CEO of Balcones Resources.
This will be Balcones’ first acquisition since Closed Loop Partners obtained a majority stake in the company in 2019. The purchase of Single Stream Recyclers is part of Balcones’ strategy to scale recycling across the United States and provide new opportunities and further sustainability initiatives for their employees, customers, and investors.
“To scale the new economic model of the future – the circular economy – we need partners committed to building models that efficiently return high value recycled commodities back into products and packaging. With Balcones Resources and Single Stream Recyclers joining forces, alongside our broad network of engaged investors, including corporate investors like Microsoft, institutional investors and family offices, together we can eliminate waste, reduce costs and increase efficiencies,” said Maite Quinn, Managing Director, Closed Loop Partners.
About Balcones Resources
Balcones Resources began operations in 1994 and has grown into a nationally recognized firm and one of the top 50 recyclers in North America. With more than 200 employees across its three locations, Balcones is a recycling partner for municipalities, multi-tenant facilities, corporate campuses, manufacturing facilities and distribution centers. For more information on Balcones Resources and its environmental services, visit BalconesResources.com.
About Single Stream Recyclers, LLC
Single Stream Recyclers is a materials recovery facility located in Sarasota, Florida. They process materials from all over the west coast of Florida. The facility sorts, bales and ships aluminum, cardboard, food and beverage cartons, glass, paper, plastics, metal and other recyclables from residential curbside and commercial recycling collection. SSR is heavily invested in technology to help create the best possible end products and reduce contamination as well as residue. Learn more at www.singlestreamrecyclers.com.
About Closed Loop Partners
Closed Loop Partners is a New York based investment firm comprised of venture capital, growth equity, private equity, project finance and an innovation center focused on building the circular economy. Investors include many of the world’s largest consumer goods companies and family offices interested in investments that provide strong financial returns and tangible social impact. Learn more at www.closedlooppartners.com.
Disclaimer:
This publication is for informational purposes only, and nothing contained herein constitutes an offer to sell or a solicitation of an offer to buy any interest in any investment vehicle managed by Closed Loop Capital Management or any company in which Closed Loop Capital Management or its affiliates have invested. An offer or solicitation will be made only through a final private placement memorandum, subscription agreement and other related documents with respect to a particular investment opportunity and will be subject to the terms and conditions contained in such documents, including the qualifications necessary to become an investor. Closed Loop Capital Management does not utilize its website to provide investment or other advice, and nothing contained herein constitutes a comprehensive or complete statement of the matters discussed or the law relating thereto. Information provided reflects Closed Loop Capital Management’s views as of a particular time and are subject to change without notice. You should obtain relevant and specific professional advice before making any investment decision. Certain information on this Website may contain forward-looking statements, which are subject to risks and uncertainties and speak only as of the date on which they are made. The words “believe”, “expect”, “anticipate”, “optimistic”, “intend”, “aim”, “will” or similar expressions are intended to identify forward-looking statements. Closed Loop Capital Management undertakes no obligation to update publicly or revise any forward-looking statements, whether as a result of new information, future developments or otherwise. Past performance is not indicative of future results; no representation is being made that any investment or transaction will or is likely to achieve profits or losses similar to those achieved in the past, or that significant losses will be avoided.
Closed Loop Partners at the United States Senate Environment and Public Works Committee on Recycling
June 19, 2020
Launched in 2014, Closed Loop Partners (CLP) is the first investment firm primarily focused on building the circular economy. Our vision is to help build a new economic model focused on a profitable and sustainable future that aligns the interests of shareholders, brands and local communities and the environment that we all share. Closed Loop Partners provides equity and project finance to scale products, services and infrastructure at the forefront of the development of a circular economy. We have over the past 5 years built a development system that connects entrepreneurs, industry experts, global consumer goods companies, retailers, financial institutions and municipalities.
On June 17, 2020, Bridget Croke, Managing Director, at Closed Loop Partners spoke at the United States Senate Environment and Public Works Committee as they held a hearing on “Responding to the Challenges Facing Recycling in the United States.” The following text is drawn from her testimony.
Today, we have over 40 investments in companies and municipal projects in the United States, all focused on helping Americans avoid landfill disposal fees while generating good jobs in the recycling and manufacturing sector. Our investors are a combination of some of the largest American based consumer brands in the world including 3M, Coca-Cola, Colgate Palmolive, Johnson & Johnson, Keurig Dr. Pepper, PepsiCo, Procter & Gamble, Unilever and The Walmart Foundation, as well as the American Beverage Association, institutional investors, family offices and environmental foundations. CLP proves that public–private partnerships are critical to unlocking the capital needed to build robust recycling and circular economy infrastructure needed to create jobs, reduce waste and build the supply chains of the future.
Despite some of the headlines we’ve all seen, recycling is big business in America and should create the manufacturing feedstock for future packaging. In 2019, the recycling industry in America generated over $110 billion in economic activity, $13 billion in federal, state, and local tax revenue and 530,000 jobs. In spite of COVID and market challenges in recent years, 2020 is shaping up to be a year of major innovations in the recycling industry as it becomes central to circular economy business models that major consumer goods companies and cities are deploying. Transitioning US manufacturing to circular supply chains could unlock a $2 trillion opportunity.
Recycling continues to be the most cost-effective option for the vast majority of American cities. The economics are simple. Cities have two choices when it comes to disposal: recycle or landfill. While the value of recycling is generally reported as the amount that a city can be paid for its recyclables, the core economic value of recycling is actually the opportunity for a city to avoid costly landfill disposal fees. Economic analysis conducted has shown that the U.S. scrap recycling industry is a major economic engine powerful enough to create 531,510 jobs and generate $12.9B in tax revenue for governments across the US.
New York City, the largest market in the United States, is an example of how advanced recycling infrastructure and strong local markets create long term profits. New York City has a long-term public-private partnership with Pratt Industries that converts all of its recycled paper locally into new paper products sold back into the NYC market. Via its contract with Pratt, New York City is paid for every ton of paper its residents recycle, as opposed to a cost of over $100 per ton to send paper, plastics and metals to a landfill.
Minneapolis is another good example. Eureka Recycling and the City of Minneapolis invested in local community outreach focused on keeping their recycling stream clean of contamination, defined as non-recyclable material. The result is one of the lowest contamination rates of any municipal recycling program in the country. With a clean stream of valuable recyclables, Eureka consistently shares with Minneapolis the profits earned from the sale of their recyclables. In many other cities, unfortunately, approximately 15% of the material that arrives at the municipal recycling facility is considered contamination. Municipal recycling programs that keep contaminants out of the recycling stream via strong community outreach or enforcement realize lower costs and better revenue opportunities. Municipalities that recognize that recycling is part of the commodities industry, not the waste industry, generate value.
Along with the examples of Pratt Industries in New York City and Eureka Recycling in Minneapolis, Recology in San Francisco and Balcones in Austin, among others, continue to provide their municipal and commercial customers robust recycling service. In addition, municipalities like Pensacola, Florida and Davenport, Iowa that manage their own best in class recycling facilities consistently reduce landfill disposal costs and create local economic value for their constituents.
The value of recyclable commodities continues to have a wide range. The cost to process municipal recyclables at a recycling facility is, on average, $70 per ton. That means that for a recyclable commodity to have value, it must have a market that pays the recycling facility over $70 per ton of that material. A sample of the commodities that are usually profitable to recycle include PET plastic (beverage containers), HPDE plastic (laundry detergent and soap containers), rigid polypropylene (bottle caps, some yogurt containers), cardboard and aluminum.
In 2020, three innovations are driving the increased profit potential of recycling in America and the development of a vibrant and growing Circular Economy.
- The introduction of robotics and artificial intelligence. The future of the industry will be led by the recycling facilities that produce the highest quality commodity bales of materials. Companies like AMP Robotics have introduced robotics (robots) with artificial intelligence systems that enable the sorting and production of high-quality commodity bales, supply chain tracking and safeguards against contamination that were never before imagined in the industry.
- Packaging innovation. We are seeing the emergence and growth of smart refillable packaging systems like Algramo that makes it cheaper and more convenient for consumers to use packaging more than one time. We are also seeing a growth in packaging that is designed to be recycled for value. Temperpack, for example, is a packaging technology that uses recycled cardboard to keep packaged food cold, replacing a significant amount of low value plastics like Styrofoam peanuts, which are both not recyclable and a common contaminant in the recycling system.
- Advanced plastics recycling technologies, including purification technologies and chemical recycling technologies. Purification is an enzymatic process that improves the quality of recycled plastics so they can more easily be used again in packaging. P&G invented a technology and helped launch a company, PureCycle Technologies, that will significantly increase the value of recycled plastic by removing color and smells. Chemical recycling is a process whereby plastic is depolymerized back to the base monomer, intermediary or carbon state in order to remanufacture a new plastic. Some plastics, like PET, HDPE and rigid polypropylene have significant value and are very profitable for the recycling industry, but they can degrade after a number of recycling cycles while some other plastics currently have limited value or are challenging to recycle. Chemical recycling has the potential to create an infinite circular economy value loop for all plastics. Some of the leading innovators are backed by major consumer goods companies. In 2020, we expect a number of emerging companies to move from pilot to commercialization phase.
These and other circular advancements are attracting significant private capital from leading investors. The industry saw investments from leading investors across asset classes. Google and Sequoia invested in AMP Robotics, Goldman Sachs is now the largest shareholder in Lakeshore Recycling Systems, Citi is largest investor in rPlanet Earth, a bottle-to-bottle plastics recycling facility in California and SJF Ventures invested in TemperPack.
The emerging leadership demonstrated by a number of retailers and consumer brands is driving the growth of the circular economy and improvements in recycling. Leadership means designing products and packaging that are free of any non-recyclable material and profitable for recycling. These packages are manufactured with recycled content, while reducing raw material inputs. Brands are telling their consumers that their commitment is to use recycled content in their packaging. Leaders are transparent in their progress, reporting in their annual reports the use of different recycled feedstocks. They know that any product or package that is not recyclable is destined for a landfill (or even worse, a river or ocean), and that cost is passed to the taxpayer.
Walmart has developed design for recycling guidelines for their suppliers to ensure the products sold in their stores are recyclable and piloting refillable packaging models. Unilever’s Seventh Generation Brand uses mostly recycled HDPE plastic in its packaging and recycled paper in its paper products. And over 10 global companies have invested over $150m in CLP’s investment funds so together we can help spur more innovation and create more tons of recycled feedstock coming through systems in the US.
We are also seeing a major trend amongst consumer goods companies looking to increase their use of recyclable material in the packaging and products they sell. It makes sense. At scale, along with the considerable environmental benefits, it should be less expensive for companies to manufacture using recycled material. That is why most major beverage companies including Coca-Cola, Keurig Dr. Pepper, PepsiCo, Nestle and Danone as well as the world’s largest consumer goods companies such as P&G, Unilever and Colgate Palmolive are publicly communicating aggressive goals for the use of recycled materials in their products and packaging.
For Americans, recycling is a matter of economic self-interest. Recycling our cardboard, paper, beverage bottles, rigid plastics containers, and aluminum cans has three important outcomes. First, it reduces the cost to manufacture the products we buy. Second, it reduces the amount of our taxpayer dollars used every year to pay landfills. Third, it generates revenue for our communities via the sale of recyclable commodities. A recent analysis reported the average cost to dispose of a ton of municipal waste in the US in 2019 was $55 per ton, and disposal fees in some states average more than $100 per ton.
Despite these economic incentives, large parts of the United States still have little or no recycling collection or processing infrastructure. Much of the economic activity generated by recycling is accomplished by long standing recycling programs on the West and East Coast as well as the upper Mid-West of America. For those who live in parts of the country with limited or no recycling infrastructure, their tax dollars are wasted on the cost of sending valuable commodities to landfill that could otherwise be sold. While the 90m tons currently recycled in the United States saves American taxpayers and businesses over $3 billion annually in landfill disposal fees, over 180 million tons of recyclable materials are landfilled, costing American taxpayers and businesses over $5 billion annually in landfills fees. We are literally throwing money in the garbage.
It is also important to recognize how China, which has received much press as of late for their role in the American recycling ecosystem, impacts the industry. For much of the past 20 years, the U.S. recycling industry was dependent on China as the leading export market. As consumption and waste has increased in China, the Chinese government has decided to develop their own domestic recycling infrastructure. This may cause some short-term pain in some parts of the United States’ recycling industry, but leading companies in the recycling industry, consumer goods and packaging industry, as well as a number of investors, see this as an opportunity to further develop and profit from domestic recycling and manufacturing infrastructure.
These are exciting times in the recycling industry as the development of the circular economy continues to expand. Major innovations are entering the industry ranging from robotics to supply chain mapping to advanced technologies that recycle plastics. Like any major industry analysis in the U.S., there is no one or two cities that should be extrapolated to define the industry. There are cities where recycling is profitable and a major economic engine and there are cities where the recycling program is struggling. What is clear is that the cities that focus on limiting contamination in their recycling program, build efficient and effective material recovery facilities and who contract with best in class recycling companies benefit from recycling programs that are both profitable and produce good local jobs.
Leading municipalities, recyclers, manufactures and brands are starting to partner together to establish, and profit from, a circular economy in the United States where goods are continually manufactured using recycled material from local recycling programs. This partnership in developing a circular economy will result in one of the largest investment opportunities in the United States over the next decade, major reduction in landfill disposal fee paid by municipalities, and become a primary driver of job creation in local economies.
We encourage policy makers to build incentives and develop policy to spur the market for recycled content and product and system innovation that reduces waste, creates jobs and makes recycled content competitive with the raw material market.
Closed Loop Partners Invests $2 Million in Reterra to Further Close the Loop on PET Plastic & Keep Valuable Materials in Play
March 03, 2020
Using advanced recycling technologies, Reterra turns discards from the plastic recycling process into high-value intermediary products.
NEW YORK, March 3 — Today, Closed Loop Partners announces a $2 million investment in Reterra, a Houston-based advanced recycling company founded in 1999. Reterra’s technology turns waste byproduct streams of PET plastic that are produced during the recycling process into high value intermediary products. In doing so, Reterra creates a market for material that would otherwise typically end up in a landfill, while also improving the overall economics of PET recycling.
With 3-6% of material lost throughout the recycling process of PET, and the demand for recycled plastic set to grow, there is a significant and growing opportunity for recapturing the discarded material from PET recyclers. Thirty seven of the world’s largest brands and retailers have made public commitments to incorporate a specified amount of recycled content in their packaging within the next ten years. This demand creates the pull through the recycling system and sends signals to packaging suppliers and manufacturers to shift their supply chains in order to include more recycled content.
“Reterra’s advanced process serves a critical role in lowering the cost of PET recycling by capturing even the smallest discards of material and making a high value product from them. This solves a system-wide issue that will become increasingly important as the market for recycled plastics continues to grow,”
Ron Gonen, CEO of Closed Loop Partners.
Reterra’s innovative technology transforms the discards into a liquid intermediary that becomes useful feedstock for a number of different applications, thus turning waste into value. The investment from Closed Loop Partners will help finance the move into their recently-acquired new facility and upgrade equipment to increase capacity and meet new customer demands. The new plant will double capacity immediately, enabling them to increase processing to almost 100 million pounds of material annually within two years.
“For the last five years we’ve been operating at capacity, but with the help of Closed Loop Partners we are now able to take our business to the next level and capitalize on the growing market demand for our products,”
Jason Ball, President of Reterra.
The investment comes via Closed Loop Partners’ Infrastructure Fund, its first project finance fund. The fund is backed by the world’s largest brands and retailers and aims to build recycling and circular economy infrastructure across the United States to better recapture materials and get them back into manufacturing supply chains.
About Closed Loop Partners
Closed Loop Partners is a New York based investment firm comprised of venture capital, growth equity, private equity, project finance and an innovation center. The firm invests in the circular economy, a new economic model focused on a profitable and sustainable future. Investors include many of the world’s largest consumer goods companies and family offices interested in investments that provide strong financial returns and tangible social impact.
Media contact: [email protected]
We Can Accelerate Solutions for Plastics & Circular Supply Chains
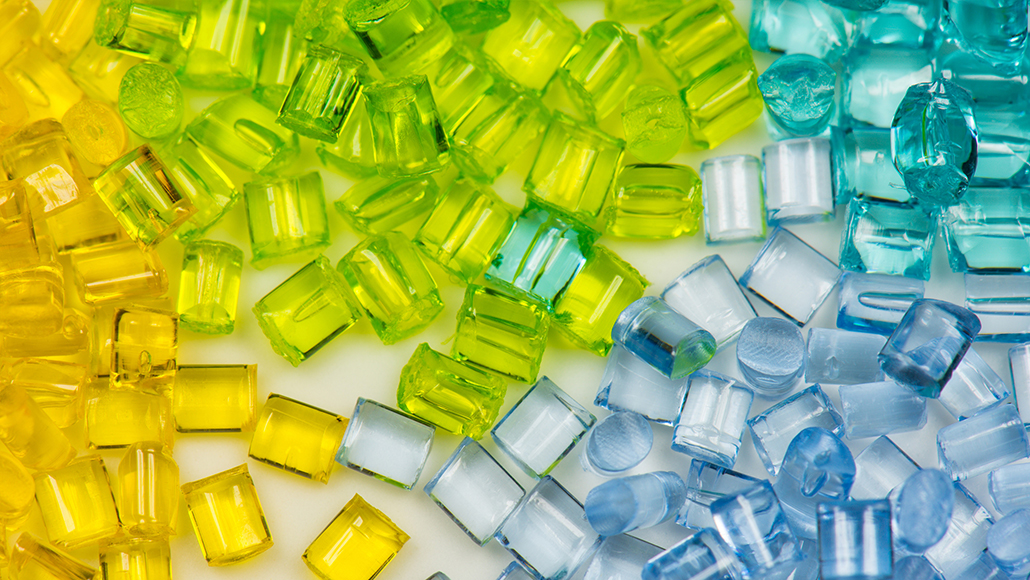
New Report Shows Tremendous Value to be Captured…. When We Stop Throwing Plastics in the Trash
The U.S. and Canada send over 34 million tons of plastics to landfills or incinerators each year. Following current trends, global plastics demand is forecasted to triple by 2050. And even more troubling, mismanaged waste leaks into our environment – there may be more plastics than fish (by weight) in our oceans by 2050.
But what if we could change that? What if we could use innovative chemical recycling technologies to purify, decompose, or convert waste plastics into the building blocks for renewed raw materials instead of discarding them after one use?
What if we could also reduce the world’s reliance on fossil fuel extraction, reduce landfill disposal costs for municipalities, decrease marine pollution, and generate billions in new revenue?
We can.
Investors and brands have an opportunity to influence and accelerate transformational technology solutions that repurpose plastics waste and keep materials in play in circular supply chains.
There are at least 60 technology providers developing these transformational technologies that purify, decompose, or convert waste plastics into renewed raw materials. This report proposes accessible, shared language to use to define and talk about each of these processes going forward:
Purification involves dissolving plastic in a solvent, then separating and purifying the mixture to extract additives and dyes to ultimately obtain a “purified” plastic. Purification processes make it possible to safely transform carpet into yogurt cups — greatly increasing the value of plastics waste. PureCycle Technologies will do just that when it opens its Ohio facility in the next year.
Decomposition is a process that involves breaking molecular bonds of the plastic to recover the simple molecules (“monomers” or “intermediates”) from which the plastic is made. In other words, plastic doesn’t just have to go back to plastic – it can become a valuable raw material to be used again. Loop Industries decomposes PET into its monomers and, with its partners, aims to produce a Loop-branded recycled PET pellet.
Conversion is similar to decomposition in that the process involves breaking the molecular bonds of the plastic. A key difference is that the output products from conversion processes are often liquid or gaseous hydrocarbons similar to the products derived from petroleum refining. These raw materials may enter different supply chains, such as fuels for combustion, and/or petrochemicals that can be made into intermediates and monomers for new plastics. Agilyx, based in Oregon, uses both decomposition and conversion technologies that can produce a variety of products, including naphtha, jet fuel, synthetic crude oil and styrene monomer, depending on the feedstock.
Through these technologies, it’s possible to recycle plastic back into plastic, AND to create valuable upstream products that keep materials in play.
The technology is possible. The question now is: How fast and how far can we go?
Every sector of society is engaged in the broad challenges of climate change and the visible problem of plastics waste. Many of the world’s largest and most influential brands are taking ownership of the problem and looking at their own supply chains. The Center for the Circular Economy at Closed Loop Partners is creating a roadmap for how to build on this momentum by unifying the diverse actors in this space and accelerating collaborative investment to bring solutions to scale.
Demand for plastics is strong and growing, yet the supply of recycled plastics available to meet demand is stuck at 6%. Options for recycling plastics today don’t capture the full opportunity: with current infrastructure, a small portion – less than 10% – of plastics waste from many consumer packages and products is recovered and recycled. Current mechanical processes and infrastructure aren’t enough to support the publicly stated goals of many global brands who have committed to use more recycled plastics in their products and packaging, or to achieve the zero waste goals of our major cities.
We surveyed more than 60 technology providers – broadly categorized as using one (or more) of three processes described above – nearly all of them at least at the lab stage of maturity, with significant potential to grow and scale. More than 40 of these solution providers are operating commercial scale plants in the U.S. and Canada today, or have plans to do so within the next two years.
But of the technology providers surveyed, it has taken them 17 years on average to reach growth scale. That’s not fast enough. More investment is needed now to accelerate these solutions – to go from “possible” to “probable”.
That’s why we are calling on investors, brands, and industry to join us in: investing to bring solutions to scale; increasing awareness of how these technologies apply to different supply chains and waste streams, including adopting the shared language from this research; and collaborating on partnerships with technology providers.
If these technologies are understood more broadly – and are more widely adopted and scaled – tremendous economic value can be realized. According to our analysis, if these technologies can meet market demands for plastics and petrochemicals, they have a potential addressable market of $120 billion ($47 billion for polymers) in the U.S. and Canada alone.
We need to stop thinking of plastics as waste, and start treating it as a resource. Until we do this, we are taking tons of value – and throwing it in the trash.
We hope you will take the time to read the full report: “Accelerating Circular Supply Chains for Plastics”. You can also see the overview of our key findings and recommendations for next steps here.
Join us: If you are interested in participating in our ongoing research, convening, and investment in this area, we encourage you to introduce yourself to the Center for the Circular Economy: [email protected].
We look forward to working together to accelerate solutions to plastics waste and circular supply chains.